As industry and government have strived to make us, as consumers, safer in the 20th and now 21st centuries, we have made great strides in reducing exposure to hazardous substances in our everyday environment. One such area wherein advances have been made in identifying potentially harmful substances is in the fields of residential and commercial construction.
For centuries, lead has been used in multiple applications for the manufacturing of goods and products that we use in our everyday lives. In many instances, we are surprised that lead resides on a list of ingredients which completes the makeup of a specific part or product. In the past two decades we have also learned that the consumption or introduction of lead into our bodies can have a very detrimental effect on our overall health. So much so that both government and industry have taken many precautionary measures to reduce the opportunity for us to come in contact with or ingest lead. In 1975 we began the process of switching to lead free gasoline and in the past decade, well documented efforts were undertaken related to the elimination of lead in paint products and the removal of existing lead based paint in public areas as well as residences when ownership changes occur.
Most recently, an effort to eliminate another source of lead exposure and intake has been undertaken for the purpose of eliminating lead in the manufacturing of brass plumbing fixtures related to potable water applications. In the past, lead was used in brass to make castings pressure tight. In the foundry process, lead is the last element to solidify and therefore seeks and fills the microscopic voids in the brass. Lead also acts as a lubricant and chip breaker during the machine operation allowing for easier machining and longer tool life.
To better understand legislation and timelines that gets us to a lead free, brass product inventory, early in 2011 President Obama signed into law Senate Bill 3874 with a timeline of three years to implement, making the new law effective on January 4, 2014. In simple terms, the Reduction of Lead in Drinking Water Act legislation amended the Safe Drinking Water Act (SDWA) to reduce the allowable lead content in brass products from 8.0% to 0.25% (weighted average). The new law applies to the wetted surfaces of any brass product used in a potable water system.
One source of confusion for professionals and consumers alike is the many different names used when people refer to the new lead free alloy. No Lead, Low Lead, Lead Free, Federalloy and EnviroBrass are just a few. Basically, everyone is talking about the same thing… Different manufacturers adopted the industry “buzz words” used in their respective market segments. There are anticipated future standards and specifications to clarify some of this industry jargon, as well as the variety of product labeling that exist today. But once again, the new federal law carries the most weight by specifically defining the allowable lead content (0.25%) of brass products in January of 2014.
Manufacturers, distributors, contractors, and water utilities all had existing inventory that needed to be depleted. There is no magic process that allows brass products containing lead to be recycled into a lead free alloy product other than through an inventory replacement process. R.C. Worst & Co. began doing so in January of 2013 and by July of this year we will have replaced the majority of our brass inventory to one of lead free. R.C. Worst & Co.’s Purchasing Manager, Paul Karnitz, committed early to the complete lead free brass inventory at the end of 2012 and believes that companies that took the initiative to do so will be able to meet the January 4, 2014 deadline of selling and installing the newly required brass product.
The basic properties, performance, and appearance of the new metals are similar to the product being sold today. However, it does require more care during every step of the manufacturing process and this does add cost. Does that mean lead free brass will cost more? Yes, lead free brass alloy products are estimated to cost 25% to 40% more than the product we manufacture and sell today. As manufacturers gain experience with the new alloys and become more efficient, we are optimistic the cost differential will diminish.
But, the immediate cost increase of lead free brass does open some doors for other metals to be specified and used. Specifically, stainless steel has suddenly moved to the top of the preferred plumbing fixtures parts list in many applications. “In the past, stainless was considered a good product but based on price comparison to brass it simply wasn’t cost effective to use”, said Karnitz. “But, with current cost increases of lead free brass and the uncertainty of future price increases, stainless steel has suddenly worked its way on to many part lists. We will have to see how this all plays out over the next few years.”
No matter what occurs in the market place related to the mandated use of lead free brass, it is a certainty that R.C. Worst & Co. will be ready for the changes in store just as we have been in other areas of product and regulation change for the past 60 years of this third generation, family owned company.
Article by Larry Jeffres
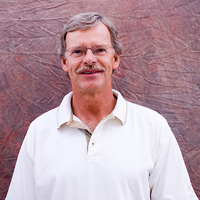